Solve, prevent or mitigate problems related to corrosion.
Corrosion Testing
The photos on this page were taken in a control room for a pulp mill and similar computer rooms that are exposed to corrosive gases produced as by-products of manufacturing. This kind of corrosion can take place where nobody can see it until it’s too late. Hidden corrosion can take place and over time cause a critical component or circuitboard to fail enough to cause serious damage in the manufacturing process. If the failure takes down a critical operation it could cost the plant millions in lost production.
That’s why it’s critical to continuously monitor air quality for corrosive gases. We recommend periodic 30-day tests using our Corrosion Classification Coupons exposed to the air in a critical space. After the test, the coupons are returned for analysis, and we send the customer a report that notes the amounts of corrosion. We include measures of copper and silver loss. We compare levels with the Instrument Society of America Standard 71.04-2013 chart of room classifications (please see below). Any result that exceeds Class G1 level is considered corrosive and measures need to be taken to remove those gases.
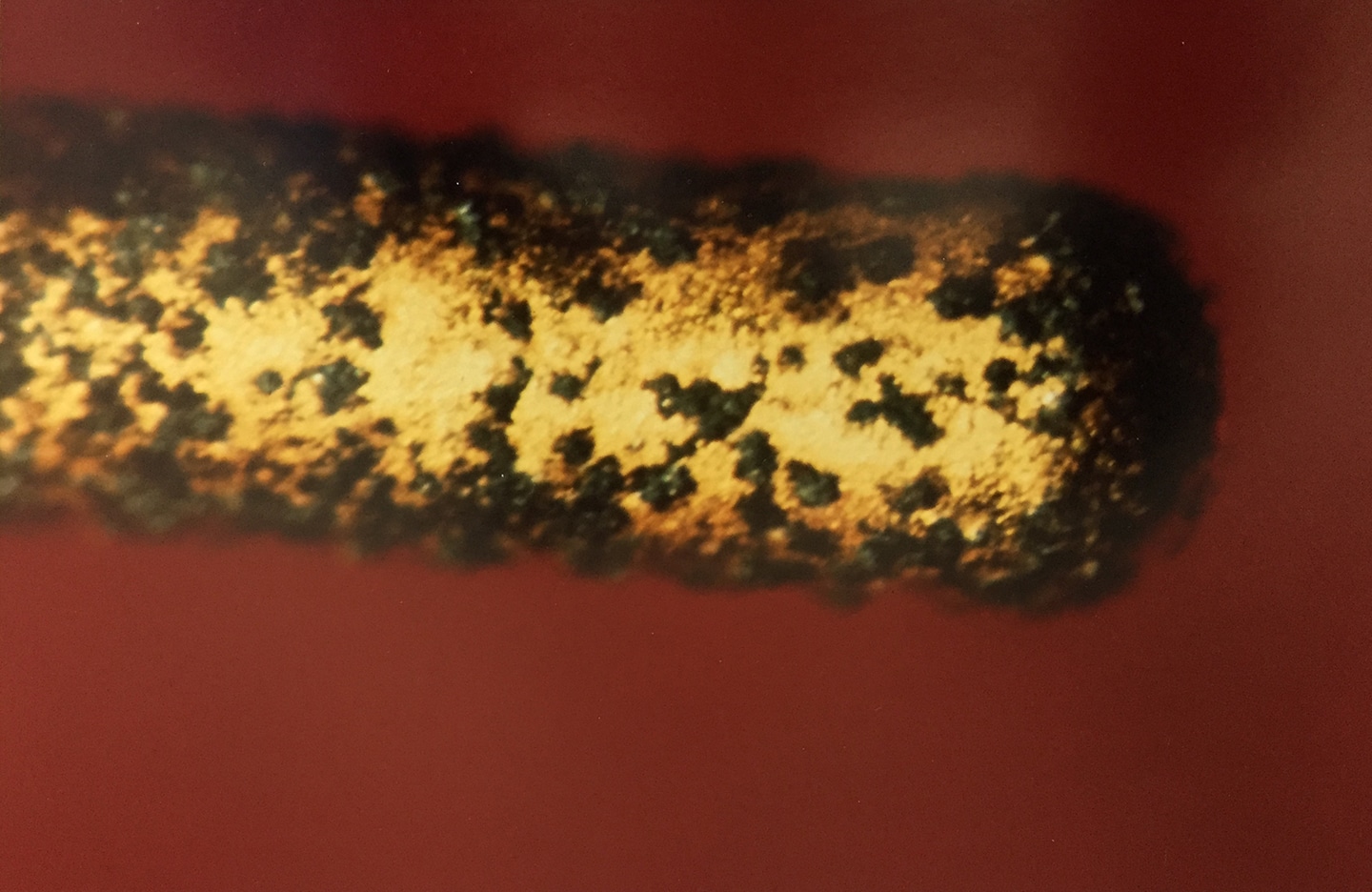
A better choice is to place within the space a real-time Environmental Condition Monitor™ (ECM). The ECM includes a display panel that indicates the conditions within the space—from Class G1(acceptable) through Class GX (extremely corrosive). Besides the LED indicators, the ECM has an alarm capability for connection to a horn, light, or computer system to alert operators to increasing levels of corrosion.